Embedded Sustainability – in search of excellence with less
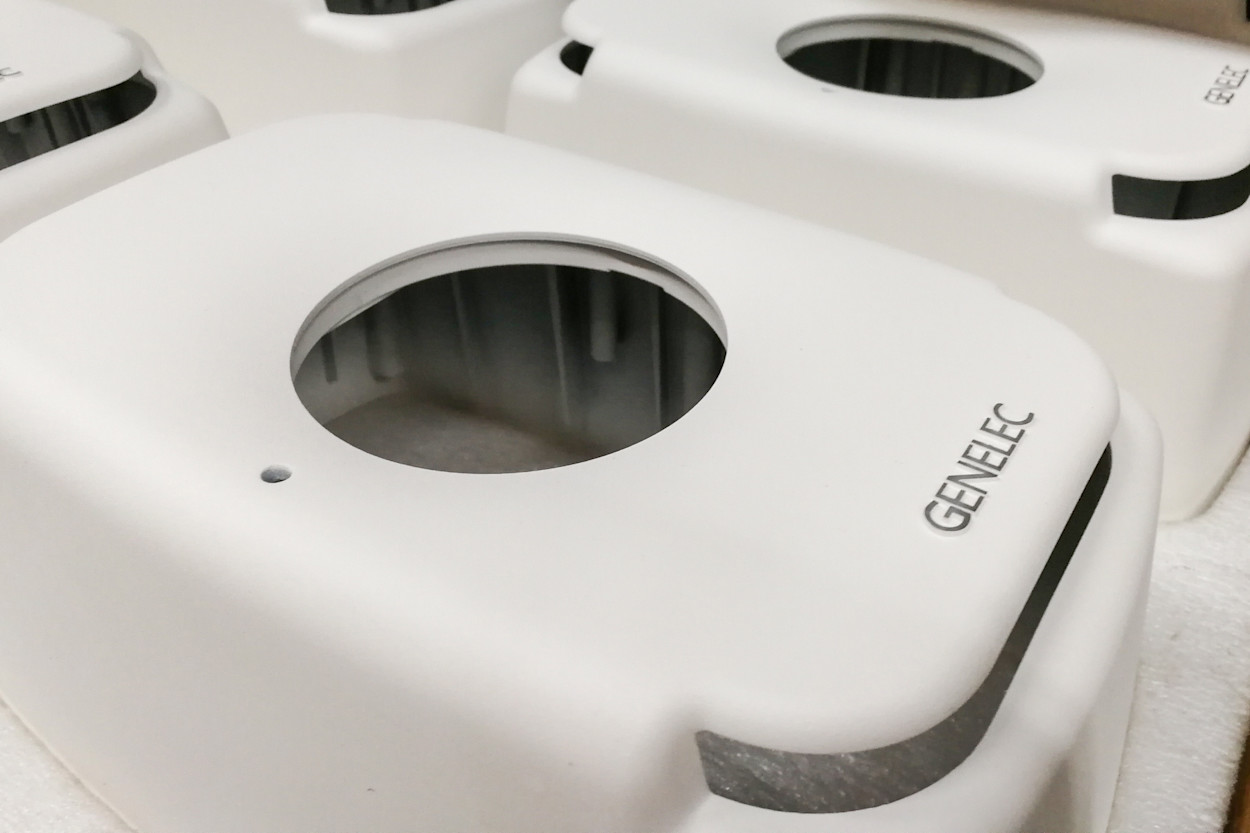
Sustainability and environmental issues are not limited to putting waste in the correct refuse sack, they are about our overall approach. At Genelec, we have always possessed a holistic attitude to our work, searching for new innovations which create more value for users, but which cost less in terms of resources.
In 2008, we entered a previously unwritten part of the company’s philosophy and heritage directly into our strategy: environmental issues are just as important as profitability. The decision came naturally and was derived from Genelec’s integral culture; for decades the creation of reliable, long-lasting products which offer excellent performance has been the cornerstone of the company’s success, and sustainability has always been embedded within the heart of our operations, philosophy and values. The practical consequence of this approach is that even the very first products from Genelec, manufactured four decades ago, often remain in active use within countless numbers of challenging professional environments worldwide. Just as importantly, we are still ready and able to support those original products with spare parts and technical support, though neither are often required.
There are of course deep reasons behind our decision to enshrine sustainability within our company plan, and also far reaching consequences. The conservation of natural resources and the efficient use of material and energy in all levels of manufacturing, transport, and during the lifetime of a product have become key concerns within our operation, on a par with innovation, efficiency in manufacturing and exceeding the standards of the global marketplace.
Our efforts have been numerous: The heating of the Genelec factory was changed from oil to renewable energy, and we chose to continue developing and manufacturing all of our products under the same roof in Iisalmi, Finland, where we can guarantee the use of environmentally efficient solutions. In our own factory, we can ensure that the highest quality thresholds are maintained in terms of operations and products, and that spare parts are available to support our users for the long-term. Ultimately, our choice has helped us to view productivity from a new and far more healthy perspective.
Since 2002, Genelec has participated in a university research project studying the use of wood composites in injection moulding. In 2006, we realised that this work showed great promise with the exploration of a wood-based natural composite material that was potentially very effective for high quality loudspeaker enclosures.
Genelec founder Ilpo Martikainen had a keen interest in sustainability
Finally, in 2009 we started a program to develop loudspeaker enclosures which comprised of at least 50% mouldable wood fibres. The results of this research were demonstrated at the HiFi Expo 2012, in Helsinki, Finland, where we introduced the Natural Composite Enclosure (NCETM), using our existing product mould for the 1029. This initiative resulted in a breakthrough loudspeaker enclosure, launched in 2013, which boasted several benefits over conventional enclosure technologies.
The resulting enclosure has many of the positive acoustical properties of wood fibres, being for example 100% stiffer than the ABS plastics typically used in loudspeaker construction. We have also eliminated the need for painting the enclosures – a potentially environmentally hazardous undertaking, the loss of which also equals substantial savings in terms of transportation and handling. Crucially, the natural composite material is recyclable and can be reused in the same manufacturing process to produce new products.
The injection moulding process facilitates the production of highly acoustically optimised shapes and forms, thereby allowing an elaborate mechanical acoustical optimisation of the enclosure design, with internal support structures that further increase the stiffness of the enclosure. In addition, the enclosure’s internal volume is maximised – a key factor in achieving high acoustic output at low frequencies.
More than 80% of our professional two-way monitoring products use recycled aluminium, saving 95% of the energy required to produce the material compared with virgin aluminium. The best example of that design and manufacturing process has been applied to our recently launched flagship three-way coaxial monitors, The Ones.
Though every action has its environmental footprint, so every action taken to improve sustainability and to reduce that footprint is a step towards reducing the impact of our industry on our environment. The conservation of natural resources does not stop with the use of recyclable natural materials, it continues throughout our efforts to create new innovations that will enrich the lives of our users. Genelec is committed to the pursuit of its ethical goals both now and in the future, when we believe that sustainability and profitability will go hand in hand.
The last two decades have, sadly enough, demonstrated to us the self-evident need for us to save our planet for future generations. Sustainability has become not just a choice, but an imperative. For this reason, recent developments in the automobile industry, in biotechnology, and in power supply and consumption, are all warmly welcomed.
Siamäk Naghian
Managing Director